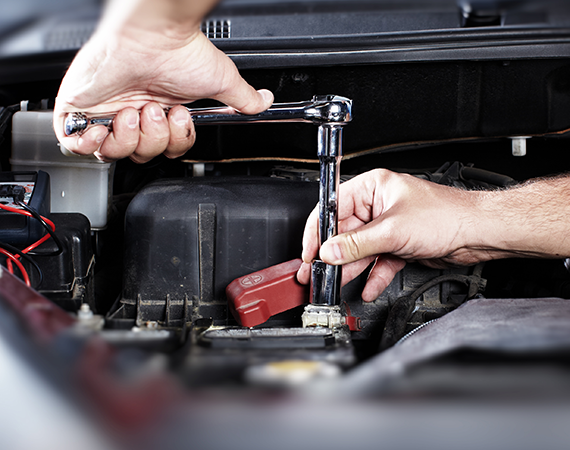
Tech Talk
We don’t profess to know everything there is to know about servicing every vehicle out there, but we’re smart enough to know there are too many to be that good. But we can say this, there are very few starters, alternators or wiper motors on engines (from cars to ATVs) that we have not removed and replaced. Our team of experts has worked hard to make Premier Gear an easy-to-do job. Premier Gear is not just for those of you that do this occasionally, but is for the working pros that need to make up time on other service projects. Our goal is to help you remove, replace, and get you back running again, without any problems (and of course, with no core to return).
Before you get started, take a few tips from our pros–it’ll help make the job go smoothly. Our Tech Tips will help you with a diagnosis – locating the right replacement part, removal of the old unit, and replacement of your new Premier Gear unit. And save the box… it will look good on your garage shelf.
Tech Tips
Starter Removal & Replacement
BEFORE REPLACING THE STARTER
A few things to know before you get started:
1. Verify the starter is nonfunctional. The starter can be tested using a carbon pile load tester, a voltmeter and clamp-on style ammeter.
2. Check and follow all safety precautions outlined in the vehicle manufacturer’s service manual.
3. Verify the batteries are fully charged and battery terminals are clean and firmly in place. Check battery cable for any corrosion or tears in the insulation.
4. Verify all fuses are good.
5. Check all wiring connections leading to the starter for discoloration, cracks, or evidence or overheating. If any of these symptoms are present, connections must be replaced. Failure to do so may result in starter or vehicle damage.
REMOVAL INSTRUCTIONS
1. Disconnect all wire connections and plugs from the starter, noting their location and identifying each connector with a piece of tape. This will make installation of the replacement starter easier.
2. Loosen the starter mounting bolts. Note the location of any shims, heat shields, and support brackets. This will also make installation of the replacement starter easier.
3. Remove mounting bolts, tilt or rotate starter to clear flywheel and transmission housing and remove starter from vehicle, noting position of any shims. Shims may be stuck to either the engine mounting or the mounting pads of the starter.
4. Inspect starter drive teeth for damaged pinions. If drive is damaged, it is extremely important that you inspect the flywheel or ring gear for broken or worn teeth (see figure below). A broken or worn ring gear must be replaced or it will damage the new starter.
Keep in mind, with Premier Gear, there is no core to return.
INSTALLATION INSTRUCTIONS
1. Check and compare the original starter to the replacement starter. All mounting holes, wire and plug connectors, and hardware should be compatible. Some vehicle manufacturers may use more than one starter manufacturer. Slight differences in the starter’s appearance will not affect the performance of the starter.
2. Install the replacement starter reusing all mounting hardware from the original starter. Refer to vehicle service manual and torque nuts and bolts to the manufacturer’s required specifications.
3. Reconnect all electrical connections of the replacement starter to the correct terminals. It is important that all connectors must be clean and fit properly.
4. Reconnect battery cable, connecting positive connections first.